モノコックボディとラダーフレーム、どちらがSUV向きなのか?
更新日:2024.09.09
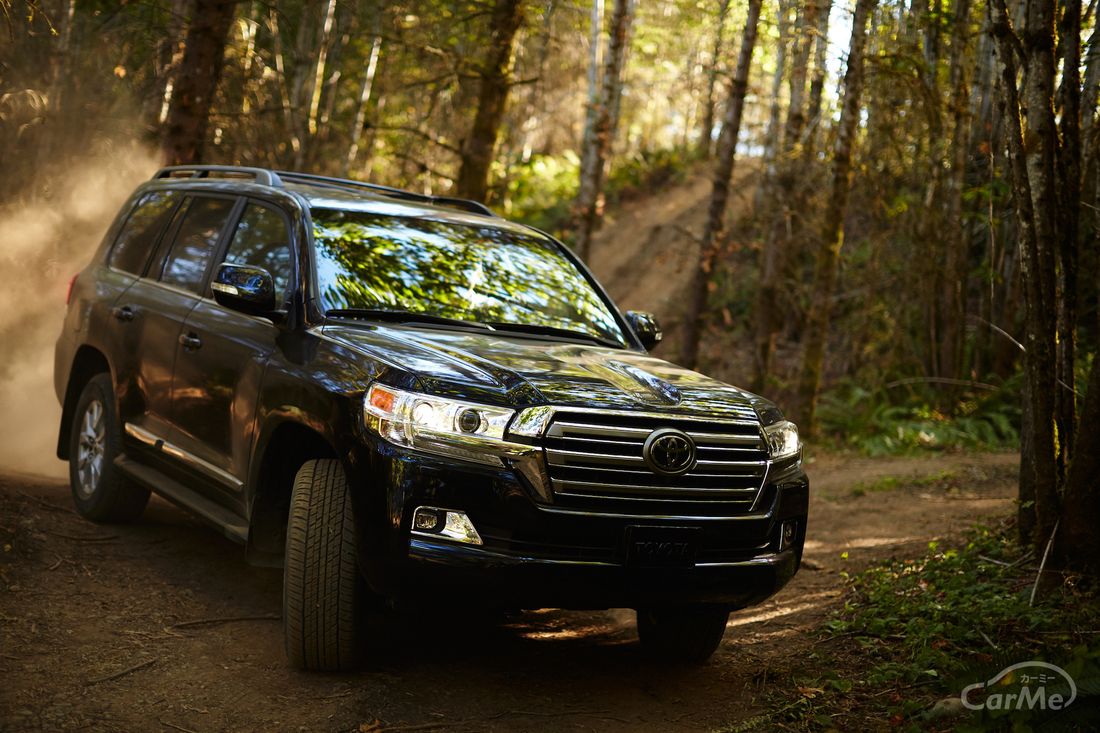
※この記事には広告が含まれます
もはやスタンダードになりつつあるカテゴリー「SUV」。そのSUVの車体と見てみると、2つの構造があることに気づきます。なぜ、同じカテゴリーでも異なるボディ構造があるのでしょうか?
ラダーフレームボディとは?
クルマのボディは大別すると「モノコックボディ」と「ラダーフレーム(はしご型)ボディ」となります。
その中間のセミモノコック(フレームインモノコック)という構造もありますが、これはどちらかというとラダーフレームボディに属すると言ってもいいでしょう。マツダ ロードスターに採用されているバックボーン構造は、1本の背骨のような補強材を持っていますが、こちらはモノコックボディに属します。
さてクルマの源流である馬車の時代から使われてきたもっともベーシックな車体構造が、ラダーフレーム構造です。
その名の通り、構造上のコアとなっているのはハシゴ形の骨格です。馬車や自動車黎明期には、木製のラダーフレームが使われていましたが、もちろん現在は金属製。この金属でしっかりとできたハシゴに、エンジンやトランスミッション、タイヤなどのパワートレイン(駆動系)を付けて、さらに別に製造したアッパーボディを載せています。
ランドクルーザーやジムニーなどの一部SUV、そしてトラック、バスがこの構造を採用しています。
その中間のセミモノコック(フレームインモノコック)という構造もありますが、これはどちらかというとラダーフレームボディに属すると言ってもいいでしょう。マツダ ロードスターに採用されているバックボーン構造は、1本の背骨のような補強材を持っていますが、こちらはモノコックボディに属します。
さてクルマの源流である馬車の時代から使われてきたもっともベーシックな車体構造が、ラダーフレーム構造です。
その名の通り、構造上のコアとなっているのはハシゴ形の骨格です。馬車や自動車黎明期には、木製のラダーフレームが使われていましたが、もちろん現在は金属製。この金属でしっかりとできたハシゴに、エンジンやトランスミッション、タイヤなどのパワートレイン(駆動系)を付けて、さらに別に製造したアッパーボディを載せています。
ランドクルーザーやジムニーなどの一部SUV、そしてトラック、バスがこの構造を採用しています。
ラダーフレームの特徴は、なんと言ってもその堅牢性にあります。鉄の頑丈な骨格が、上からの荷重や路面からの衝撃を吸収するためです。多人数乗車のバスや、たくさん荷物を積むトラックに採用されているのは、このためです。
仮になにかにぶつかったりしても、基本部分にはダメージが少ないのものメリットのひとつです。上に載っているボディが凹んでも、ラダーフレームが大きなダメージを受けていなければ、そのまま走行することができるのです。
またベースシャシーとアッパーボディが別に造れるため、製作が容易で、同時にメインテナンス・修理性に優れているという面も持っています。
その一方で、鉄の頑丈なハシゴが入っているため、車重が重くなるというデメリットがあります。また製造コストも上がり、車両価格が高くなる傾向にあります。
仮になにかにぶつかったりしても、基本部分にはダメージが少ないのものメリットのひとつです。上に載っているボディが凹んでも、ラダーフレームが大きなダメージを受けていなければ、そのまま走行することができるのです。
またベースシャシーとアッパーボディが別に造れるため、製作が容易で、同時にメインテナンス・修理性に優れているという面も持っています。
その一方で、鉄の頑丈なハシゴが入っているため、車重が重くなるというデメリットがあります。また製造コストも上がり、車両価格が高くなる傾向にあります。
乗用車でベーシックなモノコックボディ
20世紀に入り、モータリゼーション(自動車大衆化)が進むと、より生産性と収益性を上げるために、クルマのボディ構造はどんどん進化していきました。
小型乗用車は過多な堅牢性を必要としないため、重くコスト高のラダーフレームは廃されていきます。その過程で、背骨とフロアを一体化させて強度を確保した「プラットフォーム式」や、前述したボディのなかにフレームを組み合わせた「セミモノコック」などが生まれましたが、やがて技術や金属素材の進化によって、モノコックボディが誕生したのです。
モノコックとは、簡単に言えば金属の板を箱状に折り曲げて組み立てたボディの構造。この箱状ボディに直接、エンジンや駆動系を取り付けています。金属と言えども、薄い板を折り曲げて十分な強度が出るのか?とお思いの方もいるはず。
では、ティッシュペーパーの箱を思い出してください。あの箱は紙ですが、ちょっと落としたくらいで歪んだりはしません。ティッシュペーパーの箱のように、それぞれの面で衝撃や荷重を分散して、互いの張力で強度を確保しているのがモノコックボディなのです。
モノコックボディは製造が容易で大量生産ができ、ラダーフレームに対して大幅な軽量化ができるのが特徴です。軽いので性能面でも有利で、部品点数が少ないので価格を抑えることもできます。また最近では、複雑なボディデザインも可能になりました。
一方で、ボディ全体がそれほど強くないという弱点もあります。
たとえば、全体の面で衝撃を吸収しているため、ある1ヶ所にモノがぶつかったりすると、簡単に折れ曲がってしまいます。すると、全体の強度確保もできなくなってしまいます。
また、極端に強い路面からの衝撃を受けると、やはりサスペンションの取り付け部分やボディ下部が歪んでしまい、最悪の場合は走行不能になってしまうのです。
さらに大きなダメージを受けてしまった場合は、ラダーフレームのように一部を交換するだけというわけにはいきません。特に最近のレーダーやカメラを使ったアクティブセーフティシステムを装備したクルマは、微妙なボディのズレでシステムが作動しない場合もあるため、より高い修理技術が要されるようになっています。
小型乗用車は過多な堅牢性を必要としないため、重くコスト高のラダーフレームは廃されていきます。その過程で、背骨とフロアを一体化させて強度を確保した「プラットフォーム式」や、前述したボディのなかにフレームを組み合わせた「セミモノコック」などが生まれましたが、やがて技術や金属素材の進化によって、モノコックボディが誕生したのです。
モノコックとは、簡単に言えば金属の板を箱状に折り曲げて組み立てたボディの構造。この箱状ボディに直接、エンジンや駆動系を取り付けています。金属と言えども、薄い板を折り曲げて十分な強度が出るのか?とお思いの方もいるはず。
では、ティッシュペーパーの箱を思い出してください。あの箱は紙ですが、ちょっと落としたくらいで歪んだりはしません。ティッシュペーパーの箱のように、それぞれの面で衝撃や荷重を分散して、互いの張力で強度を確保しているのがモノコックボディなのです。
モノコックボディは製造が容易で大量生産ができ、ラダーフレームに対して大幅な軽量化ができるのが特徴です。軽いので性能面でも有利で、部品点数が少ないので価格を抑えることもできます。また最近では、複雑なボディデザインも可能になりました。
一方で、ボディ全体がそれほど強くないという弱点もあります。
たとえば、全体の面で衝撃を吸収しているため、ある1ヶ所にモノがぶつかったりすると、簡単に折れ曲がってしまいます。すると、全体の強度確保もできなくなってしまいます。
また、極端に強い路面からの衝撃を受けると、やはりサスペンションの取り付け部分やボディ下部が歪んでしまい、最悪の場合は走行不能になってしまうのです。
さらに大きなダメージを受けてしまった場合は、ラダーフレームのように一部を交換するだけというわけにはいきません。特に最近のレーダーやカメラを使ったアクティブセーフティシステムを装備したクルマは、微妙なボディのズレでシステムが作動しない場合もあるため、より高い修理技術が要されるようになっています。
どちらのボディ構造がSUVに向いているのか
ここまで、それぞれのボディ構造についてお話してきましたが、ようやく本題に入りましょう。いまやセダンよりもクルマのベーシックなカタチになりつつあるSUV。このSUVは、モデルによってボディ構造が異なります。
そもそもSUVは、ピックアップトラックの荷台にFRP製のシェルを付けていたのが源流。北米では居住スペースによって税金が異なるため、若い人には税金の安いピックアップトラックが人気でした。ところが、荷台は雨ざらしになり防犯性も良くないため、そこのシェルを被せて使い勝手を向上させたのがSUVの始まりです。
そもそもSUVは、ピックアップトラックの荷台にFRP製のシェルを付けていたのが源流。北米では居住スペースによって税金が異なるため、若い人には税金の安いピックアップトラックが人気でした。ところが、荷台は雨ざらしになり防犯性も良くないため、そこのシェルを被せて使い勝手を向上させたのがSUVの始まりです。
日本ではハイラックス・サーフやテラノといったモデルがSUVの元祖ですが、どちらもピックアップトラックをベースにしていたため、ボディはラダーフレームでした。
ですが、時代がより高い燃費性能と運動性能を求めるようになると、SUVのボディ構造はセミモノコックやモノコックといった普通乗用車と同様のボディへと変わっていきます。
現代のSUVは二極化しています。十分な悪路走破性を持ったモデルと、日常域での性能を重視したモデルです。
ですが、時代がより高い燃費性能と運動性能を求めるようになると、SUVのボディ構造はセミモノコックやモノコックといった普通乗用車と同様のボディへと変わっていきます。
現代のSUVは二極化しています。十分な悪路走破性を持ったモデルと、日常域での性能を重視したモデルです。
ランドクルーザーシリーズやジムニーなどのオフロードSUVは、国内外で優れた悪路走破性と堅牢性が評価されており、その結果、代々ラダーフレームを踏襲しています。
日本でも山奥に行くと激しいオフロードがありますが、こうした場所で簡単にクルマが歪んで走行不能になってしまっては、時として命の危険に関わります。だからこそ、激しい衝撃にも十二分に耐えうるラダーフレームが必要となるのです。
日本でも山奥に行くと激しいオフロードがありますが、こうした場所で簡単にクルマが歪んで走行不能になってしまっては、時として命の危険に関わります。だからこそ、激しい衝撃にも十二分に耐えうるラダーフレームが必要となるのです。
一方でハリアーやヴェゼルなどの乗用車ライクなSUVは、その使用シーンのメインを舗装路としており、なかには2WDモデルさえあります。
オフロードSUVのようなスタイリングですが、その十分な最低地上高は雪道やちょっとしたダート路を走ることしか想定されていません。そもそも、激しいオフロードを走ることは考えられていないのです。それよりも、優れた運動性能や燃費が重視されているため、モノコックの方がかえって好都合というわけです。
オフロードSUVのようなスタイリングですが、その十分な最低地上高は雪道やちょっとしたダート路を走ることしか想定されていません。そもそも、激しいオフロードを走ることは考えられていないのです。それよりも、優れた運動性能や燃費が重視されているため、モノコックの方がかえって好都合というわけです。
エクストレイスやフォレスターのようにモノコックながら、CMなどで優れた悪路走破性を謳っているモデルもあります。これらはオフロードシーンを考慮した電子制御4WDシステムで悪路走破性を高めています。
またプジョー3008などもモノコックでFFながら、電子デバイスで悪路走破性能を実現。未開のジャングルや砂漠を進み続けるというのは苦手でも、一応全地形の走破を標榜しています。この全地形型のSUVは、これからのクルマのスタンダードとなりうるものです。
つまり、どちらのボディ構造がSUVに向いているのかということではなく、そのモデルが指向する走行シーンによって、向き不向きがあるということです。
やがてはラダーフレームの強度に匹敵するボディ構造が考案され、しかも運動性能も燃費もすべてにおいて優秀なSUVが登場する、そんな未来は、そう遠くないことなのかもしれません。
またプジョー3008などもモノコックでFFながら、電子デバイスで悪路走破性能を実現。未開のジャングルや砂漠を進み続けるというのは苦手でも、一応全地形の走破を標榜しています。この全地形型のSUVは、これからのクルマのスタンダードとなりうるものです。
つまり、どちらのボディ構造がSUVに向いているのかということではなく、そのモデルが指向する走行シーンによって、向き不向きがあるということです。
やがてはラダーフレームの強度に匹敵するボディ構造が考案され、しかも運動性能も燃費もすべてにおいて優秀なSUVが登場する、そんな未来は、そう遠くないことなのかもしれません。
山崎友貴|Yamazaki Tomotaka
四輪駆動車専門誌、RV誌編集部を経て、フリーエディターに。RVやキャンピングカー、アウトドア誌などで執筆中。趣味は登山、クライミング、山城探訪。小さいクルマが大好物。