フォージドコンポジット技術とは?ランボルギーニの車両重量999kgを実現した!?
更新日:2024.09.09
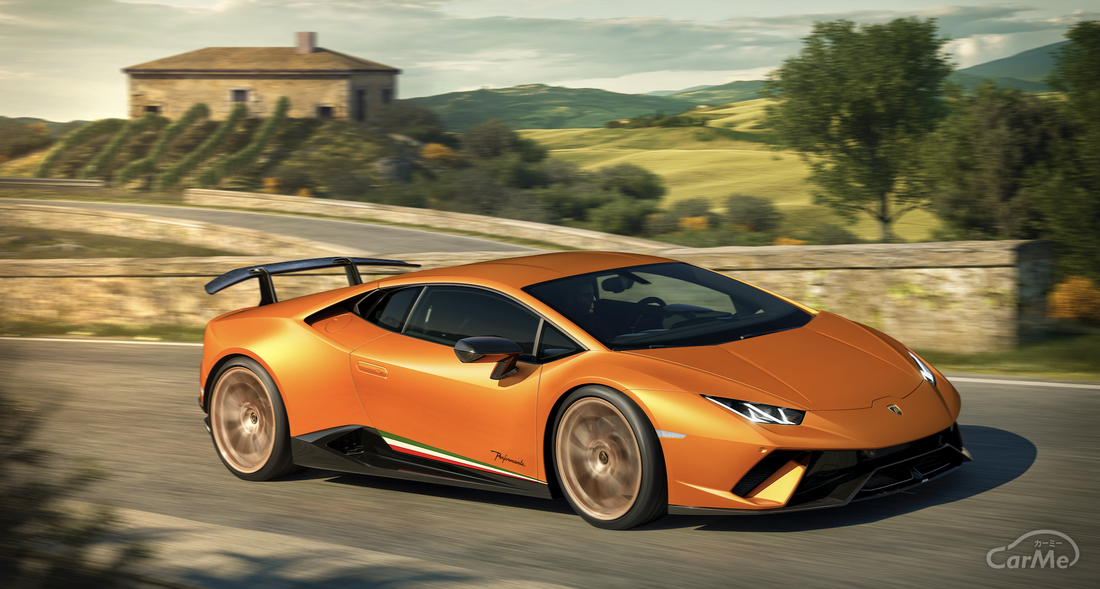
※この記事には広告が含まれます
高価な素材としておなじみのカーボン繊維ですが、いまやスポーツカーのみならずエコカーにも採用される時代。しかし、ランボルギーニが、キャロウェイ、名古屋工業大学との提携により開発された新技術「フォージドコンポジット」の登場で、これまでのカーボン素材は時代遅れになると言われます。フォージドコンポジットとは、いったいどんな特徴をもっているのでしょうか?
フォージドコンポジット技術は異業種との共同開発で誕生
「フォージドコンポジット」は、ランボルギーニ、キャロウェイ、名古屋工業大学の共同開発から誕生した新しい素材です。
ちなみに、名古屋工業大学では、2013年に日本オートモービル・ランボルギーニ先進複合材構造研究所(Automobili Lamborghini Advanced Composite Structures Laboratory Japan【ACSL Japan】)を設立。
米シアトル・ワシントン大学のランボルギーニ先進複合材構造研究所所長 パオロ・フェラボリを研究教授として迎えたACSL Japanでは、フェラボリ氏が開発した、炭素繊維と樹脂の複合材料を金型を用いて軽量な炭素繊維複合材部材を短時間に量産する技術(フォージドコンポジット技術)を中心に自動車や航空機関係などさまざまな企業と共同で次世代材料のCFRPの研究・開発を行っています。
ちなみに、名古屋工業大学では、2013年に日本オートモービル・ランボルギーニ先進複合材構造研究所(Automobili Lamborghini Advanced Composite Structures Laboratory Japan【ACSL Japan】)を設立。
米シアトル・ワシントン大学のランボルギーニ先進複合材構造研究所所長 パオロ・フェラボリを研究教授として迎えたACSL Japanでは、フェラボリ氏が開発した、炭素繊維と樹脂の複合材料を金型を用いて軽量な炭素繊維複合材部材を短時間に量産する技術(フォージドコンポジット技術)を中心に自動車や航空機関係などさまざまな企業と共同で次世代材料のCFRPの研究・開発を行っています。
フォージドコンポジット技術で生み出される素材の特性
フォージドコンポジットは、金型に入れた炭素繊維にエポキシ樹脂などを浸みこませ、130℃に加熱し60barの圧力でホットプレスする手法で作られます。複雑な形状のパーツでも簡単に作れるのが画期的と言われています。
また、通常使われるプリプレグオートクレーブ成型では6時間程度かかるところ、フォージドコンポジットではわずか9分以下で生産が可能。コスト面でも通常のカーボンに比べ30%も抑えることが可能になるという技術なのです。年々その技術は進化しており、生産時間もどんどん短縮されています。
また、通常使われるプリプレグオートクレーブ成型では6時間程度かかるところ、フォージドコンポジットではわずか9分以下で生産が可能。コスト面でも通常のカーボンに比べ30%も抑えることが可能になるという技術なのです。年々その技術は進化しており、生産時間もどんどん短縮されています。
フォージドコンポジットを採用する車種は?
わずか20台限定が市販されたセスト エレメントは、フォージドコンポジットの採用によって、5.2LのV10パワーユニット、フルタイム4WDを搭載するにも関わらず、車両重量は999kgを達成。
419kW(570ps)/8000rpmの最高出力と、540Nm/6,500rpmの最大トルクから、1.75kg/psという衝撃的なパワーウェイトレシオをマークし、0-100km/h加速2.5秒という性能を発揮します。
また、2017年に発売されたウラカン ペルフォルマンテにも同技術が採用されています。
一般的なカーボン製品は薄いシートを積層して作られますが、この新素材はごく短いカーボン繊維とレジン(樹脂)を高圧で成型(恒温鍛造)したもので、チタンの3分の1の軽さで同等以上の曲げ強度があるとのことです。強度、厚さ、形状など設計自由度が大きいのも特徴です。
ちなみに共同開発のメンバーであるキャロウェイのクラブヘッドにも採用されています。最初に採用されたのは2010年に発表された新ブランド「レイザー」です。世界最大級の自動車ショー「パリモーターショー」にて発表されました。
419kW(570ps)/8000rpmの最高出力と、540Nm/6,500rpmの最大トルクから、1.75kg/psという衝撃的なパワーウェイトレシオをマークし、0-100km/h加速2.5秒という性能を発揮します。
また、2017年に発売されたウラカン ペルフォルマンテにも同技術が採用されています。
一般的なカーボン製品は薄いシートを積層して作られますが、この新素材はごく短いカーボン繊維とレジン(樹脂)を高圧で成型(恒温鍛造)したもので、チタンの3分の1の軽さで同等以上の曲げ強度があるとのことです。強度、厚さ、形状など設計自由度が大きいのも特徴です。
ちなみに共同開発のメンバーであるキャロウェイのクラブヘッドにも採用されています。最初に採用されたのは2010年に発表された新ブランド「レイザー」です。世界最大級の自動車ショー「パリモーターショー」にて発表されました。
他社のCFRP(炭素繊維強化プラスチック)の開発状況は?
高性能CFRPはトヨタやBMWなどでも開発が進められています。カーボンファイバーは極めて丈夫な素材で、強度はスチールの約10倍、重量は約25%と、アルミニウムを遥かに凌ぐ高い強度と軽量化効果が得られるため、クルマの骨格に採用した場合、燃費が約40%以上改善すると言われています。
すでにBMWのi3やi8、レクサス LF-Aでは、ボディ骨格にCFRPが採用されています。また、東レやトヨタ、東京大学の他、日産、ホンダ、三菱、スズキ、名古屋大学等も加わってCFRPを全面採用した車の開発が進んでいます。
フォージドコンポジットは、わかりやすく言うと刀などで使われる”鍛造”技術のカーボン版です。生産量が増えればコストも安くなりそうですね。
すでにBMWのi3やi8、レクサス LF-Aでは、ボディ骨格にCFRPが採用されています。また、東レやトヨタ、東京大学の他、日産、ホンダ、三菱、スズキ、名古屋大学等も加わってCFRPを全面採用した車の開発が進んでいます。
フォージドコンポジットは、わかりやすく言うと刀などで使われる”鍛造”技術のカーボン版です。生産量が増えればコストも安くなりそうですね。